Always more, always faster, always further everything needs to arrive at the right time at the right place – the global goods cycle keeps the economy running and is a challenge for everyone involved. This only functions through the use of extensive automation within the logistics chain, which would be unthinkable without an armada of high-performance micromotors. These motors often need to generate considerable forces under extremely confined conditions and, above all, must always work reliably in continuous operation. This is why drives from FAULHABER can frequently be found in these challenging applications.
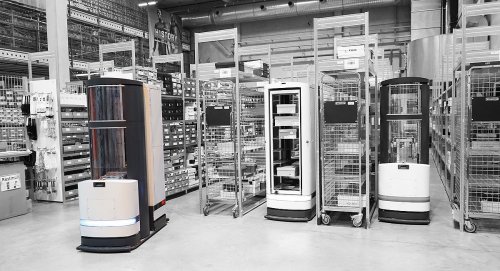
Toru Logistic Robot
Despite sounding similar and being closely related, the term “logistics” does not originate from the same ancient Greek root word as “logic”, but rather from French military jargon. Since the end of the Middle Ages, the “maréchal de logis” – the quartermaster – was responsible for providing marching and fighting troops with somewhere to sleep and rest. The quartermaster’s range of tasks grew with time and began to extend to many other parts of the overall supply chain. So what started out as simply providing “logis”, i.e. accommodation, became extremely complex military logistics.
The quartermasters originally belonged to the cavalry because the transmission of information has always been key to logistics. Until the 19th century, horses were used to relay information as fast as possible. Nowadays, electromagnetic waves that are propagated through the ether and along cables perform this task somewhat more quickly. Today, the largest data volumes are transmitted using fibre optic cables. They form the backbone of the global logistics network: The cables pass on the necessary information by means of light signals – from the online order, through shared just-in-time production in smart factories to express doorstep delivery.
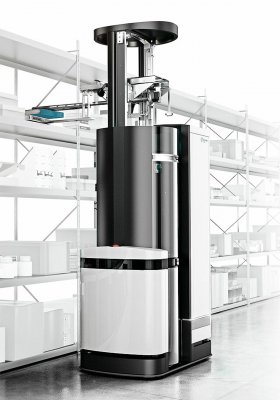
Toru Robot
Connections with nanometre precision
Two fibre optic cables must be joined together fibre for fibre. This is extremely delicate work because each individual optical fibre is as thin as a human hair. The optical core is even thinner and has a diameter of just five microns.
When two such optical fibres are joined together, the two ends must line up precisely with each other so that the signal can then later be transmitted cleanly without impairment. On construction sites, the precise alignment is carried out by small mobile machines. The individual fibre ends are first cut to length with an exact 90 degree cut, the protective insulation is stripped away and the fibres are then placed in the device. The device automatically and accurately aligns the two pieces with each other in three dimensions so that the flat ends meet precisely. They are welded together and then insulated again. Connection of the fibres and unimpeded flow of the signals are now guaranteed. The nanometre-precise alignment is performed by means of positioning drives from FAULHABER, e.g. with DC-micromotors of the 1524…SR series, with gearhead and lead screw as well as a high-resolution encoder. Drives that work with high-precision stepper motors are also used here.